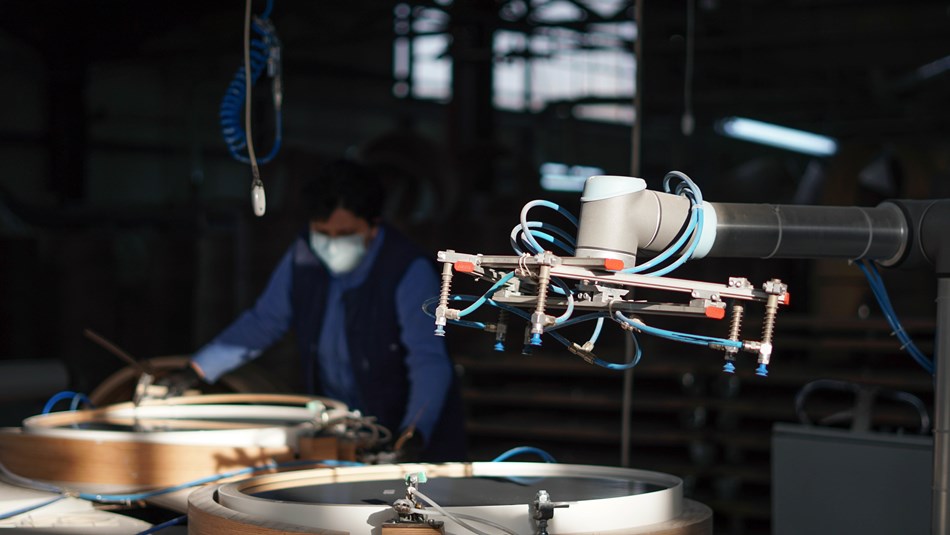
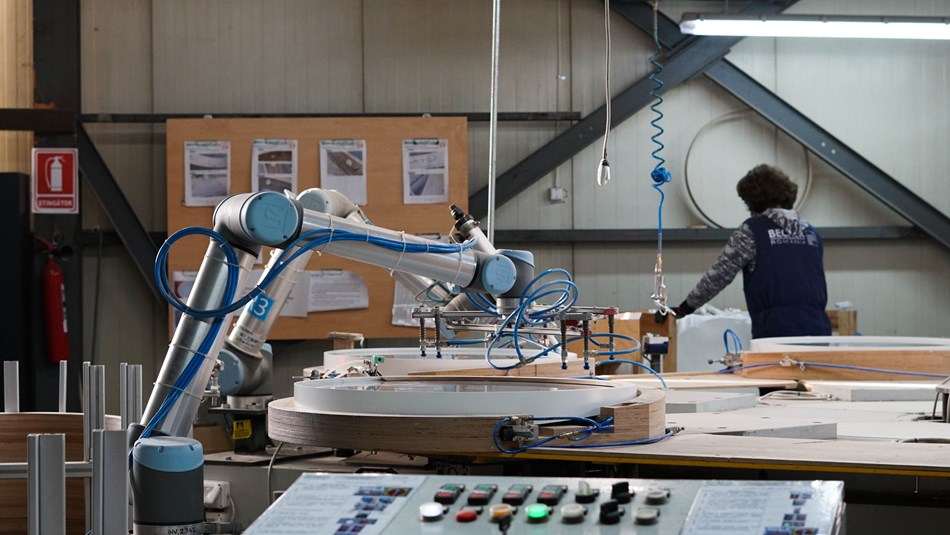
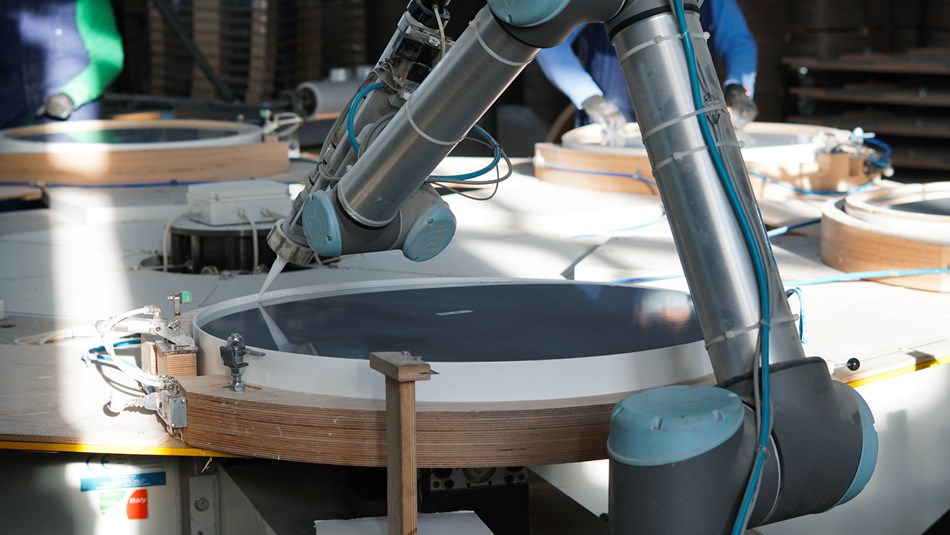
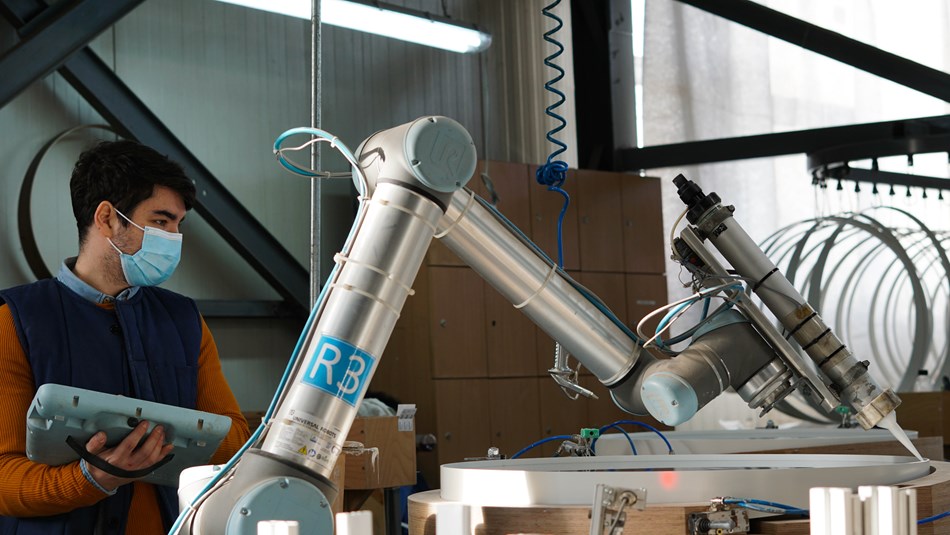
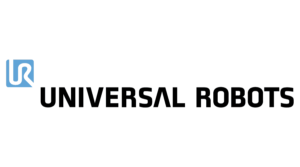
Becker Romania Palletizing Solution
By automating the glue dispensing and assembly processes with UR10 collaborative robots, BECKER Romania increases productivity.
Story
Molded beech veneer components are produced by the furniture business Becker Romania. Becker Romania has introduced two UR10 cobots to boost the productivity of repetitive labor operations without compromising the quality of the finished product. Over 10,000 cubic meters of beech wood are processed annually in Becker’s production area, where the collaborative robots conduct pick and place and glue dispensing tasks.
Challenge
Becker Romania struggled to recruit suitable workers for the production procedures in its facility, which prompted the business to investigate automation. In order to boost productivity and efficiency in the assembly process, the organization desired a collaborative automation setup in which humans and newly integrated technologies cooperate. Additionally, Becker wanted to make the workplace better for workers who would be performing more interesting and imaginative activities.
Solution
Becker Romania decided to automate with collaborative robots from Universal Robots because they can be swiftly deployed and are specifically made to safely share a workstation with people without the need for additional safety guarding. In order to assemble mirrors, two UR10 cobots are used. The first UR10 applies adhesive to the product frame, and the second UR10 adds another component—a ring segment—on top of the glue over the glass. The cobots were simple and quick to program. The business used the pre-built application CircleMove with a loose orientation towards the circle from the UR interface.
“UR collaborative robots are easy to program. You don’t need an advanced computer and automation knowledge. Anyone with minimal technical knowledge can successfully create applications with these robots,” said Remus Țopan, Technical Engineer at Becker Romania.
The seamless integration of the cobots was greatly aided by the technical help offered by Universal Robots.
“On the Universal Robot website you can find all the information you need, even backup files for the programs developed that are easy to save through the magic files on the website, and for the software updates. There is a whole community behind it, ready to help you with the answers you need,” Remus Țopan added.
Currently, the business is assembling one of its products utilizing two collaborating robots and human operators. During the mirror assembly process, the operators install the frame, the glass, and empty the carousel. The first cobot applies adhesive where it is needed using a soldering gun. A unique software made with the help of a global variable and a consumption rule alerts one of the operators when it’s time to change the glue.
“After calculating the consumption norm, we created a global “installation variable” that remains saved even if the robot is turned off. By checking it at the beginning of each program, the variable tells us if the adhesive in the tube has reached the end. When it reaches 0 the program calls a subprogram that moves the robot arm to a position that allows operators to easily change the adhesive,” explained Remus.
The second UR10 takes the second part from a semi-automatic feeding unit and inserts it on top of the adhesive using a gripper with suction cups that is simple, quick, and straightforward to construct. The cobot’s control box now contains all automation and sensors, making it very simple to program. In the warehouse, proximity sensors were utilized to find the frame and photoelectric sensors to find the ring segment. A PLC, which also manages the carousel’s operation, facilitates the link with the UR10 cobots using analog signals sent in both directions.
Benefits
The UR cobots have significantly improved product assembly quality for Becker Romania, allowing for control over the applications and repeatability of the processes. Another advantage is the cobots’ adaptability, which makes them ideal for switching to other activities as needed and which Becker views as a competitive advantage. In preparation for redeploying cobots, the business is currently testing a UR16 robot for brushing surfaces.
“UR collaborative robots are easy to be programmed. You don’t need advanced computer and automation knowledge to be able to program them. Anyone with minimal technical knowledge can successfully make applications with these cobots. We accomplished the actual programming of the pick and place application without problems in one day…” REMUS ȚOPANTechnical Engineer BECKER ROMANI