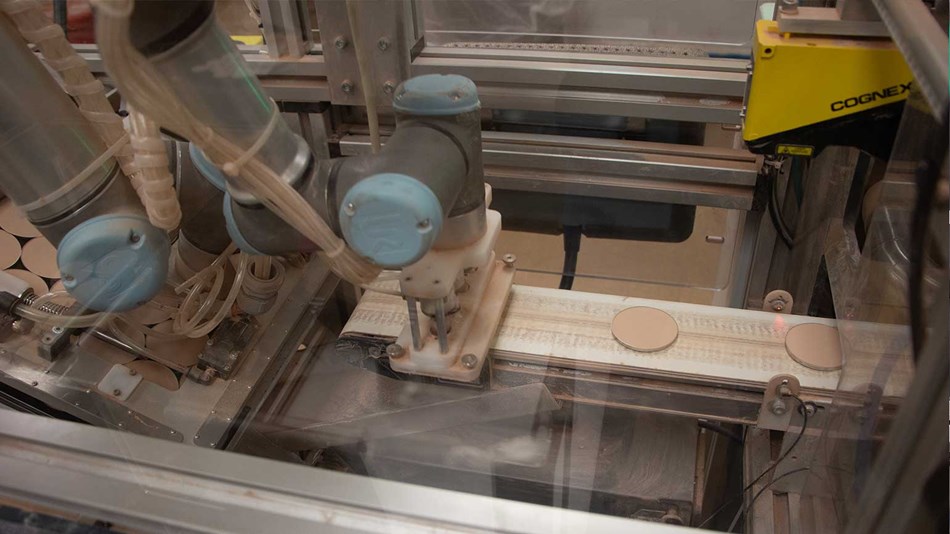
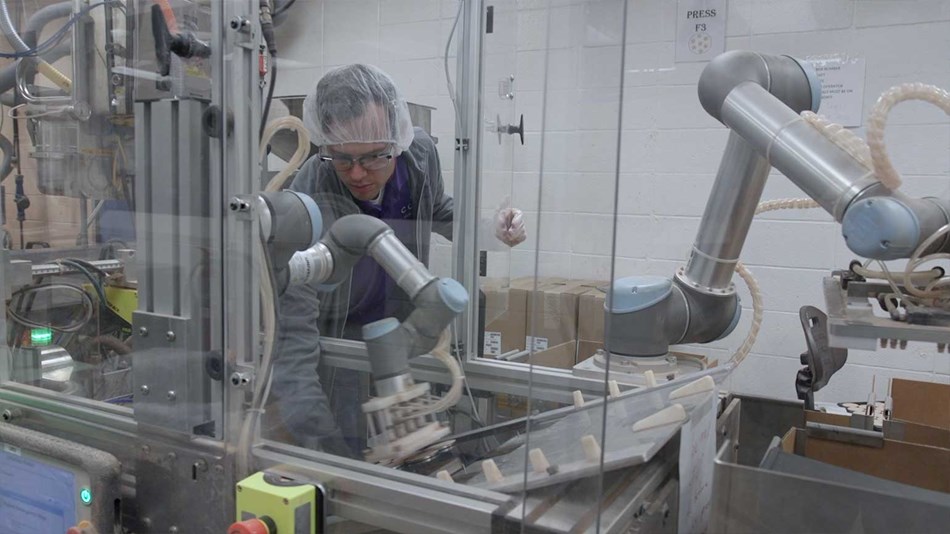
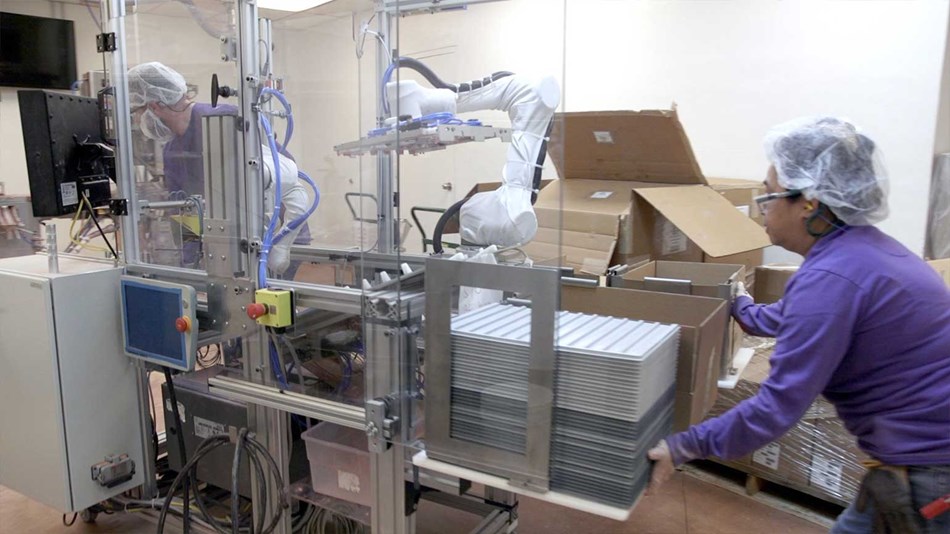
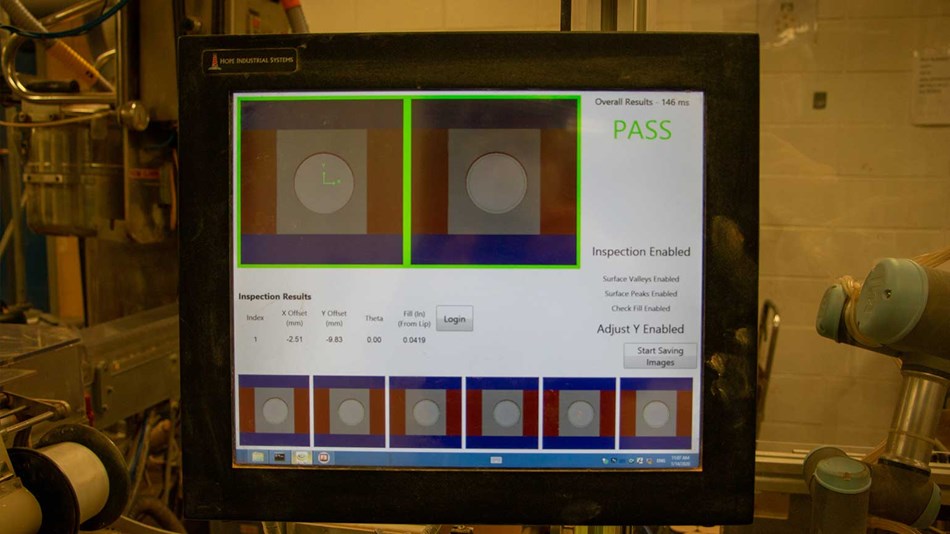
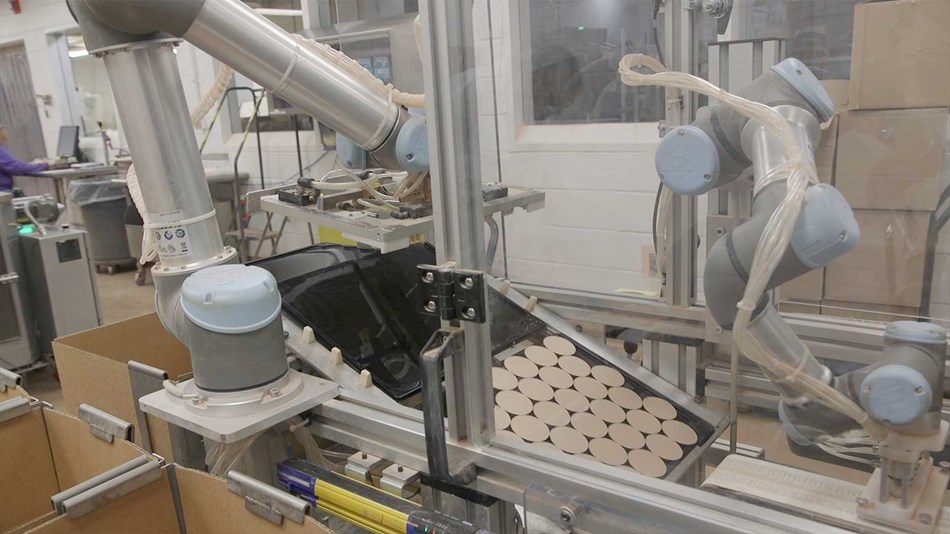
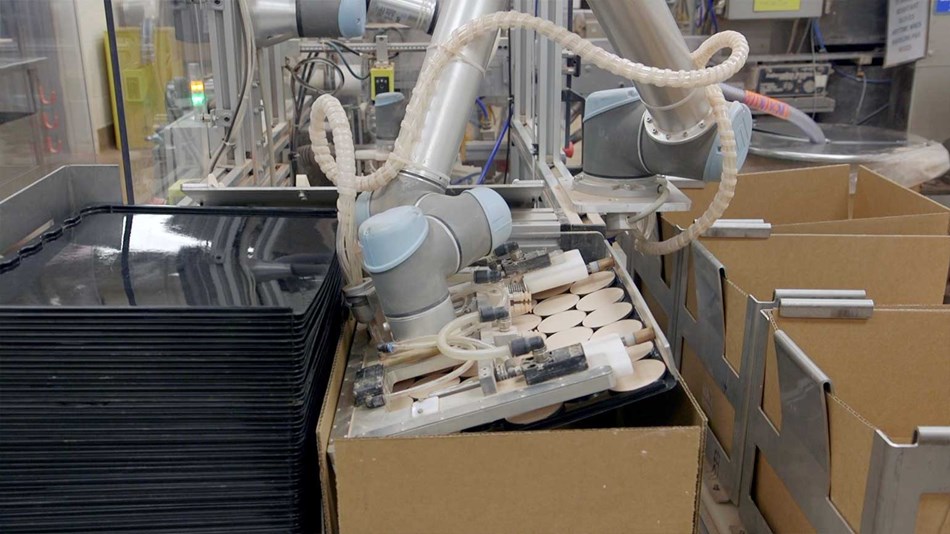
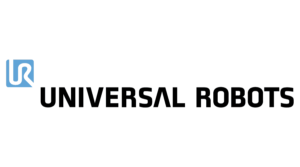
Coty Cosmetics Palletizing Solution
Coty Cosmetics saves half a million dollars annually thanks to Universal Robots.
Story
Sally Hansen, Rimmel, and CoverGirl are just a few of the well-known brands created by Coty, a global leader in cosmetics. Eight Universal Robots on four movable carts now automate the selection and packing of goods at the powder presses at the company’s factory in Maryland. The mobile solution enhances quality inspection and the working environment for employees while saving $500,000 annually.
Challenge
For Paul Baublitz, project manager at Coty Cosmetics, the issue was clear: “We currently have twelve presses, and the challenge with automation is always how do you—in a cost-effective manner—automate such a large operation?”
The repetitious nature of the task, which was not ergonomically suitable for human operators, and Baublitz’s need for enhanced efficiency were only two of the many reasons the company decided to automate. Coty had previously considered automating this operation, but it discovered that the technology on hand at the time wasn’t adequate to the intricacy of the application.
Baublitz brought the problem to Chris Sydorko, owner of the integration firm Sydorko Automation, who says, “The challenge for me was to try to determine how I could build a robotic system that was mobile enough to meet their automation needs while still being cost-effective enough to meet their budgetary needs.” Traditional industrial robots are not easily moved around due to safety regulations, which meant that Coty would have to permanently place a robot at each of the 12 presses. This was not within budget.
Solution
Instead, Sydorko looked to collaborative automation. “The Universal Robots seemed a great platform,” he says. “They’re lightweight, they’re easy to use, they’re low voltage, and certainly could work together in the same environment as individuals, so we decided to give the Universal Robots a shot.”
Picking up “godets”—metal pans containing powder cosmetics products—and placing them on trays wrapped in boxes before sending them to another department for further processing constitute the application. Powder is forced into the godets in the presses, where it is examined for surface flaws and measured for pan volume before passing beneath a Cognex 3D profiler head. A UR3 cobot picks up the godets in groups of two or four, depending on the product, and deposits them on a tray if they pass inspection. A UR5 cobot picks up the tray when it is full, transports it to one of five case locations, and then inserts the tray into the case. After that, the UR5 cobot walks to the area where empty trays are kept, picks one up, and puts it back in the tray staging area while it waits for the next tray to arrive in front of the UR3 as it loads.
Mobile cobots support fast changeovers for wide product mix
Up to ten different product “recipes” for various godet shapes, which can range from round to square or rectangular, as well as various thicknesses and weights, are now run by the cobot-based carts. These products can be produced one or two at a time. The carts can hold up to 20 different product “recipes.”
The application had significant issues with setup and switching times. Coty was able to put a UR3 and UR5 cobot on each of four mobile carts that can be moved from one press to another thanks to Universal Robots. It is significantly less expensive than having robots manning twelve distinct stations, according to Baublitz. It enabled a project that had previously been financially impossible to become feasible. For the project to proceed, having them transportable was essential. The mobile cobots typically only require 15 to 30 minutes of setup time to relocate, unplug, and set up at a new press.
“Cobots on mobile carts are much more cost-effective than having twelve different stations each with a fixed robot. It made a project go from not being possible from a financial standpoint to being possible.” – PAUL BAUBLITZ, Project Manager, Coty Cosmetics
Fast ROI, improved work environment and improved quality
Coty anticipates future savings from this cooperative automation effort of half a million dollars every year. Coty has also noticed additional advantages, but that is a sizable return on investment.
The area where the robots operate is dusty, noisy, and vibrates a lot because of the big presses. Coty may now relocate employees away from this setting and reassign them to less monotonous and more exciting activities because the robots are now operating close to these sources. According to Baublitz, “There will be thirteen fewer personnel working in that region once this solution is entirely done and operating three shifts, five days a week, with four carts. The crew is quite thrilled about the adjustment because it will significantly increase efficiency for the organization.
Baublitz also points to new quality initiatives that the Cognex inspection system adds to the automated work cells. Previously, this was one of many tasks that operators performed. “Now there’s a computer doing all of that work,” Baublitz explains. “If you see something that needs to be improved, you can immediately react.”
Safety despite high production speeds
Robots used in collaborative environments are built to work safely alongside people. However, Coty had to exceed the robots’ collaboration speed and force limits in order to maintain the necessary production speeds. Sydorko incorporated thin plexiglass protecting and light curtains as operator protection. These don’t restrict the carts’ movement, but as soon as a worker opens a door or enters a busy space, the robots slow down to a safe collaborating speed. The robots continue moving at their top pace as soon as the employee closes the door or exits the light curtain.
“You can go as fast as you need to and make sure you can keep up production rates, but you can also be collaborative if that makes more sense. It’s the best of both worlds,” says Sydorko, who often gets asked why he chose chose Universal Robots rather than a high-speed traditional industrial robot for the Coty application. One of the key reasons is that traditional robots don’t run off a low-power source. “Right now, we’re running the carts off 110 volts,” he says. “We would have to use 240 or 480 volts to run a traditional industrial robot. It gets challenging when you want to move carts and puts operators at higher risk.” The weight of a traditional high-speed robot was also a factor as well as the size of the control platforms.
Collaborative integration process leads to success
Now that the cobot-based system is set up, however, the Coty team is able to manage it internally. “If there’s ever any troubleshooting that’s needed, the integrator that we worked with is always a phone call away,” says Baublitz. “But at this point, we’ve been running with the carts for months and we’re comfortable enough that we can troubleshoot 99 percent of the issues in-house.”