
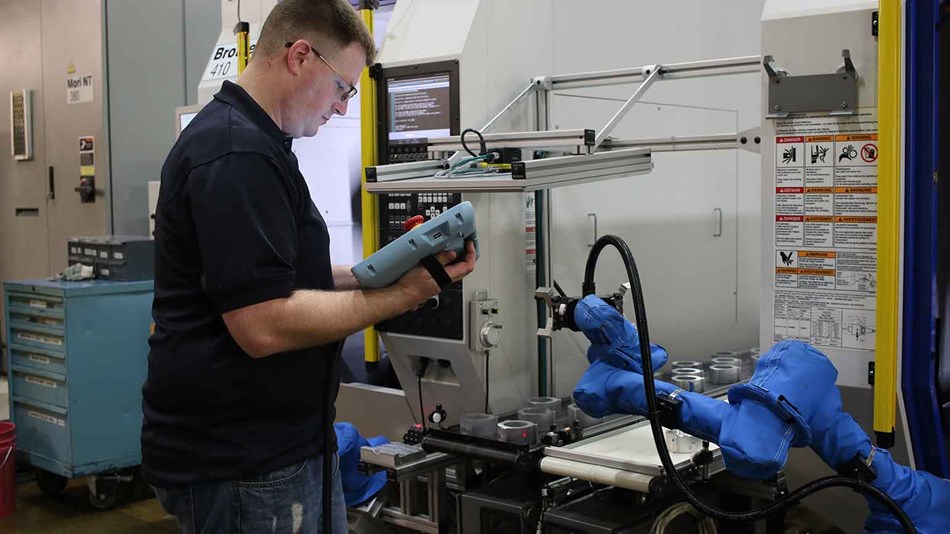
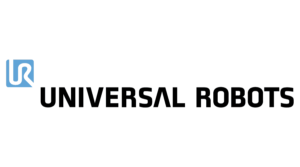
Task Force Tips Machine Tending Solution
Vision-guided collaborative robots produce firehose valves with a quick payback on investment.
Story
Keeping spindle time high and product quality constant, Task Force Tips, a producer of firefighting equipment, intended to promote and utilize their workers tending machining cells into more difficult jobs. Four collaborative UR robots with flexible task deployment were the answer.
Challenge
Since 1990, Task Force Tips in Indiana has combined robots with machine tools. However, those robots couldn’t be relocated to other machines and were devoted to working just on the one they were placed with:
“So what happens is the machine wears out first and now you have a $100,000 robot that you can’t do anything with. We had heard of collaborative robots that could be used in a much more flexible manner, so we decided to explore this new technology,” says CEO at Task Force Tips, Stewart McMillan.
Solution
A fourth UR5 robot is mounted on a table on wheels and transported between duties. Task Force Tips placed one UR10 robot, two UR5 robots, and two UR5 robots to manage CNC machines. An example of what McMillan refers to as “a profound paradigm shift”:
“A major impediment in the past to using robots was the security fencing required around the machine. The beautiful thing about the UR Robots is you don’t need all that guarding. We can roll the table with the robot right up to the machine and in a few minutes teach the robot to load parts.”
Production Supervisor at Task Force Tips, Cory Mack explains how the UR robots have reduced staffing requirements from seven to three operators:
“Now it only takes about one hour per operator per shift to operate the robot, which includes laying out parts and staging the robot. That means the robot is running for 21 hours unassisted, so we’re looking at savings of just about 34 days to pay for the robot” – CORY MACK, Production Supervisor
The Work of UR5 Robots
Having the two UR5 robots collaborate has also improved output. The first UR5 robot utilizes vision guidance to recognize and select blanks as they are placed on an inbound conveyor before placing them into the first milling machine. The UR5 then removes the partially machined component that is now in the lathe and gives it to the other UR5. The cycle is completed when an operator sets the components onto anodizing racks after the second robot has removed the finished machined item from the second machine and placed it on the outgoing conveyor.
Automation Specialist for Task Force Tips Adam Hessling describes the procedure as being highly impressive but being deceptively simple to do. He describes himself as a “journeyman machinist” without any particular background in robotics programming. The UR robot controller’s MODBUS communication protocol registers are used for both robot handoff and visual guiding.
The UR5’s force detection system will determine if the unmachined part is misshaped, has saw cut burs, or has machining chips in the chuck jaws when it is placed in the lathe.
“When the robot tries to reach the set waypoint for placement and there’s an obstruction which causes the force on the end of arm to exceed 50 Newton; which I programmed as the threshold, it knows something is wrong,” says Hessling who has programmed the robot to then apply an air blast to try and clean whatever debris is in the way.
The robot will repeatedly run the item through the air blast, and if that doesn’t work, it will instruct the machine to run a “chuck wash” cycle to clear debris from the chuck jaws using the high pressure coolant system. The popup asking the operator to clean any debris from the chuck jaws and push continue shows on the robot’s touchscreen if the part still cannot load after the coolant wash. Another window that completely stops the software appears if the problem continues. After determining the issue, the operator can resolve it and resume production.
“I would estimate that the robot fixes the “failure to load” issue about three or four times per hour, which has really helped us eliminate downtime. The operator only needs to intervene about once per shift, sometimes never,” explains Hessling.
The improvement of product quality has also been significantly impacted by releasing employees from machine tending.
“When our employees are not worried about keeping a machine running all the time, they have a lot more time to visually inspect the machined products. Part quality has really gone to a whole other level with the UR Robot in place, while allowing our personnel to come up with new ideas and better ways to improve our production,” says the TFT Production Supervisor, who is now testing the UR robots in deburring, packaging, and laser machine applications.